Process
How Homes Are Built
Consulation
Controlled Factory
& More
Installation
Final Finishings
STEP 1
Initial Client Consultation
Clients meet with one of our knowledgeable and experienced retail members to begin discussions around the scope of the home. Budget, size, style preferences, building processes and more are agreed upon. Contracts are reviewed and then begins the process of the architectural drawing and building phases.
STEP 2
Framing Inside Controlled Factory
During the same time site preparations are taking place (to build the foundation in which to place the home), the home begins to take form within a quality-controlled factory. Here professional tradespeople work in stations along a series of assembly lines to create components for the framework of your home that will eventually be installed at subsequent stations within the factory at the exact time they are needed within the homes building process. This efficient right-on-time method of building drastically reduces material waste, wait times for product shipping and wait times for qualified staff to arrive on site to complete their portion of the build as all materials and staff are readily available and on-site within the factory to complete their stage of the home when required.
STEP 3
Fixtures, Floors & More
Dissimilar to site-built homes, exterior walls and trusses for rooflines are not installed until the final stage of the homes build, allowing carpenters, plumbers and electricians easy access to work within the homes framework to install the homes internal systems. Furnaces, water heaters, fixtures and floor coverings are all installed at this stage.
STEP 4
Wall & Roof Installation
Finished interior and exterior walls, flooring and trusses have been pre-created with absolute precision within subsequent assembly rooms are now fastened into place. A continues air/vapor barrier is installed, along with interior drywall while the home rests securely within a one of a kind jig.
STEP 5
Transportation & Final Finishings
After passing final inspections, your home is now prepped for transport and loaded upon a certified transport truck to be brought to your location. Your home will be seamlessly transferred from the truck and assembled on-site where final finishings will be completed.
On average, most Modular Homes can be built in the factory in 2-4 weeks. Because Modular Homes are built indoors, weather delay is never a problem. From the time the home arrives on site, it takes approximately another 2-4 weeks for the builder to complete the home.
* Due to impacts on building material availability, timelines have changed to 8-12 months from build to on-site completion.
Because modular homes are transported to the site, they are engineered to a higher standard of strength than stick-built homes. Pieces are nailed/screwed and glued to add strength to the structure and make our modular homes more durable against the adverse effects of Mother Nature.
Homebuilders and homeowners have the same ability to create a custom home with modular construction. There are hundreds of modular home plans to choose from with options to design the custom style you want. Hardwood floors to Corian counter tops, you can choose from thousands of upscale personalized features to fit your budget and taste.
The consolidation of labour and most building materials at a housing/building factory, usually within 150 KM of the building site, results in reduced car/truck traffic. The time frame for building is drastically reduced therefore noise, pollution, and quality of life for future neighbours is minimized.
Climate controlled factory conditions and assembly line procedures optimize insulation & air/vapour barrier installation, resulting in a tighter and better insulated envelope that requires less energy to heat & cool. This means harmful weather never touches the inside of the home.
Benefits
The Future is Modular

Proud Supporters of the Ronald McDonald House Charity
We are proud supporters of the B.C. Ronald McDonald House. With every home sold in British Columbia, a donation is made to Ronald McDonald House.
LEARN MOREFactory-Built Method
Revolutionizing the Home Building Process
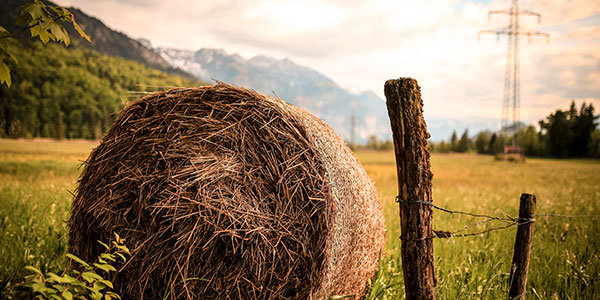
Rural Properties
Pre-manufactured, yet highly customizable modular housing options are a practical, economical and sustainable choice for your rural property.
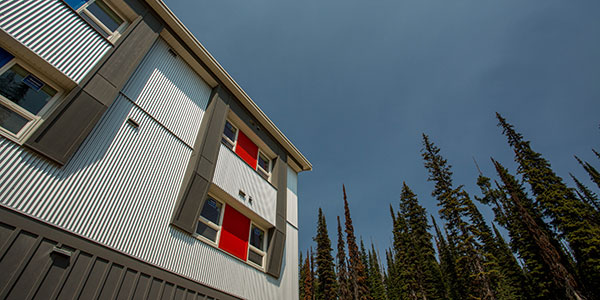
Multi-Family
Modularly-built communities are master-planned and architecturally designed similarly to how any on-site built residence would be, however, all building is done within a quality-control manufacturing plant and then erected on-site in a matter of days.
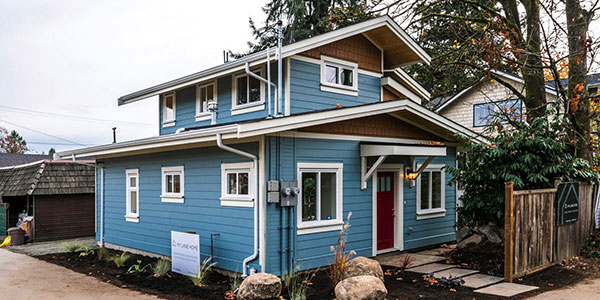
Laneway Homes
Laneway homes are typically erected at the rear of an existing property on existing vacant land or can be built to replace a current structure such as a garden shed, carport or detached garage.
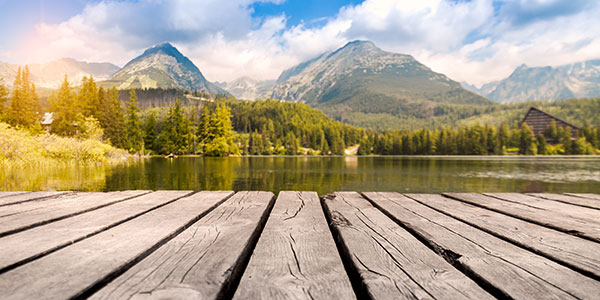
Recreational Property Homes
You have found and possibly purchased your dream recreational property, away from the hustle and bustle …and possibly also a ways away from a local contractor, access to building supplies and trades.
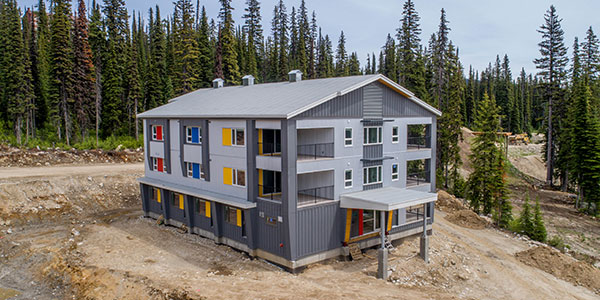
Social Housing
Modular multifamily housing construction can increase the development of healthy affordable housing by saving significant cost, time, and resources.
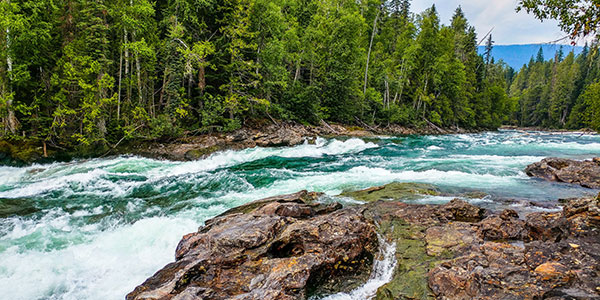
Environmental Advantages
Climate controlled factory building procedures ensure optimal insulations and vapor barrier installation. This provides a better insulated product that requires less energy to heat and cool.
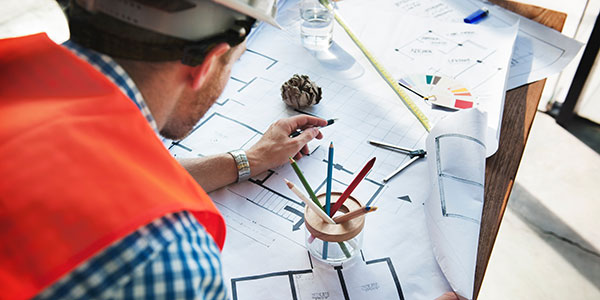
Advantages for Developers
Modular construction poses a number of potential competitive advantages for commercial developers.
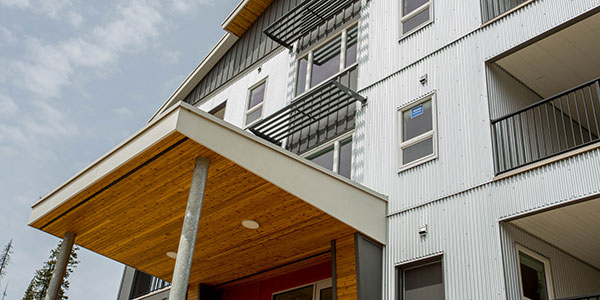
Advantages for Municipalities
With a long list of benefits, it is understandable why modular built communities are a growing trend!
Industry News
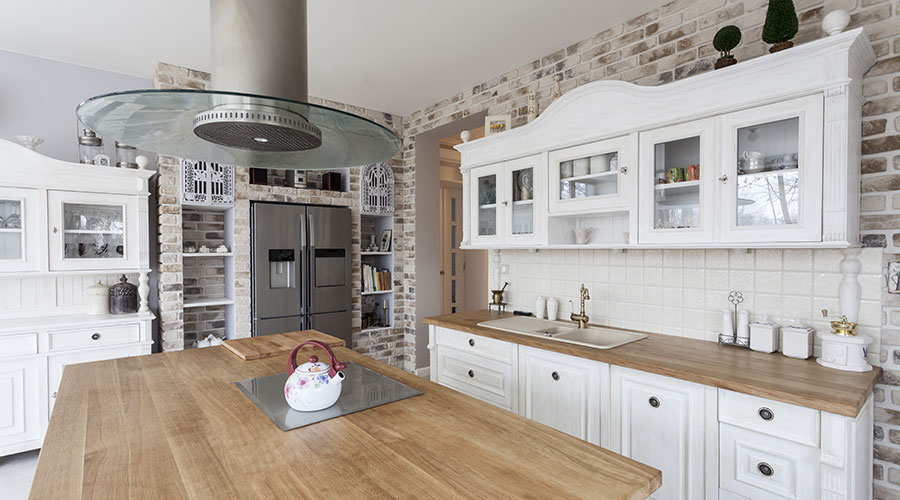
Press Release: MHABC Applauds Vancouver’s Natural Gas Amendment for Attainable Housing
July 26, 2024
The Northern Flickee – Seamlessly Blending Innovative Building Techniques with Modern Comforts
May 14, 2024
Chateau De Vine - Sustainably Built for Longevity and a Brighter Tomorrow (Naturally)
May 14, 2024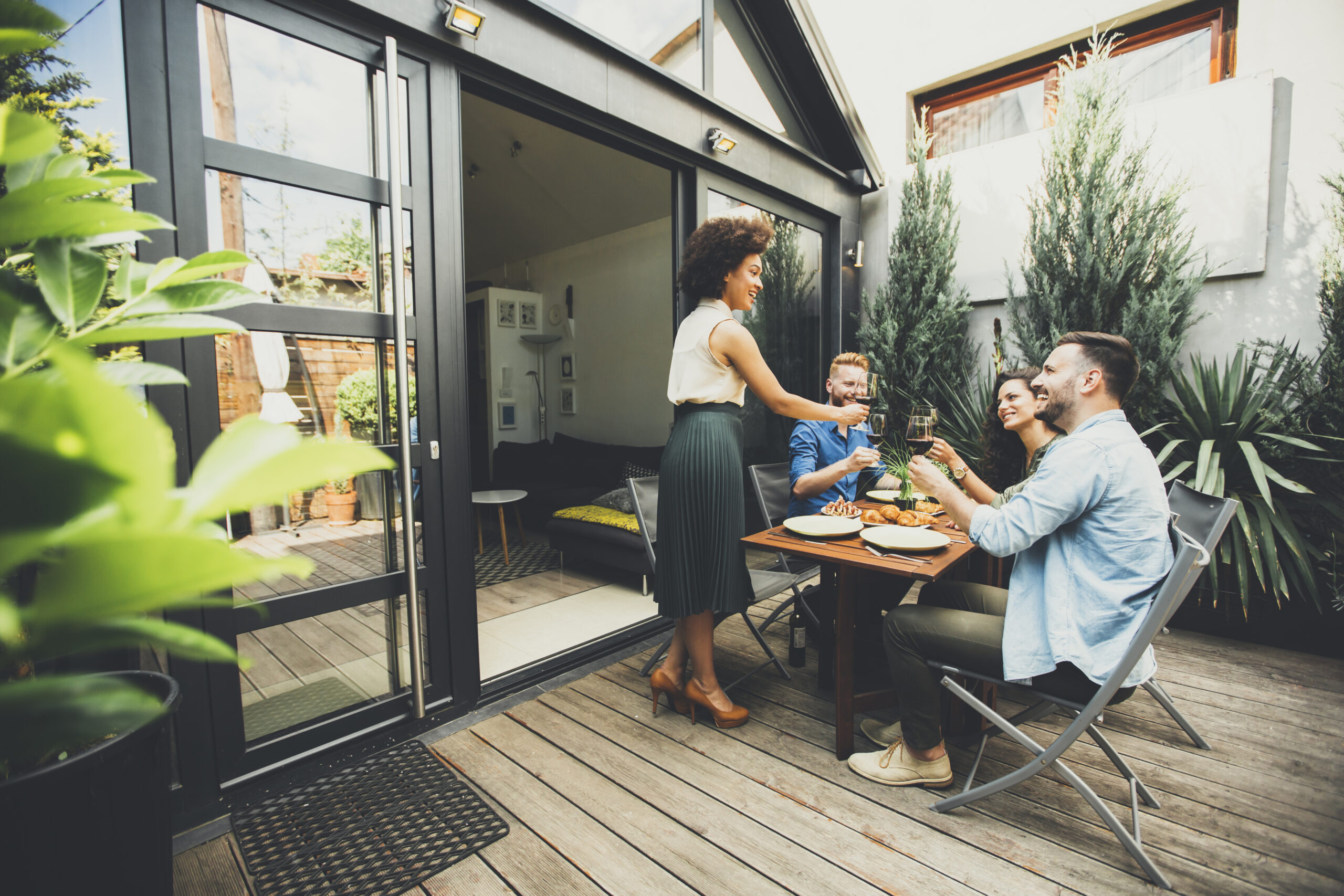